Unveiling the Secrets to Finding Quality Suppliers for Best CNC Machine Service
In today's highly competitive manufacturing landscape, the demand for high-quality CNC machine service is paramount. According to a recent industry report by Grand View Research, the global CNC machine market size is expected to reach $100 billion by 2025, growing at a CAGR of 6.2%. This rise is indicative of the increasing reliance on precision engineering and customization in various sectors, including aerospace, automotive, and medical devices. However, sourcing reliable suppliers for CNC machine services can often feel overwhelming. With numerous options available, identifying the ones that consistently deliver quality can be challenging. This guide aims to unveil the secrets behind finding top-tier suppliers, ensuring that your CNC machining needs are met with precision and efficiency, thus enhancing your operational capabilities and overall business success.
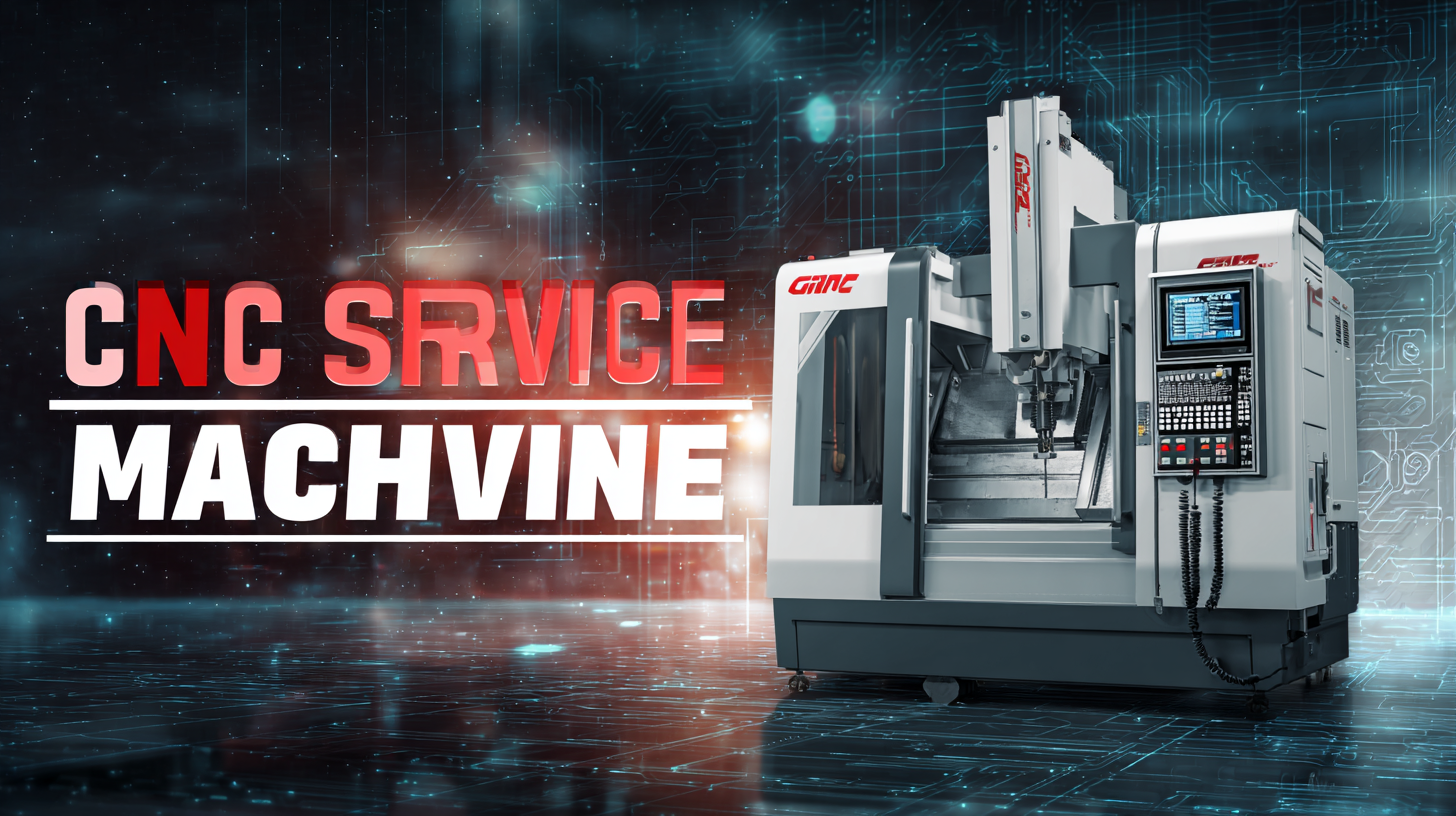
Understanding the Evolution of CNC Machine Services in 2025
As we advance into 2025, the landscape of CNC machine services continues to evolve at a remarkable pace, primarily driven by technological innovation and industry trends. According to a report by MarketsandMarkets, the global CNC machine market is expected to reach $100 billion by 2025, growing at a CAGR of 6.2% from 2020. This growth reflects not only the rising demand for precision engineering but also the shift towards automation in manufacturing processes. Companies are increasingly seeking suppliers that leverage the latest CNC technologies, such as AI-driven machining and IoT-enabled machines, to optimize production efficiency and reduce downtime.
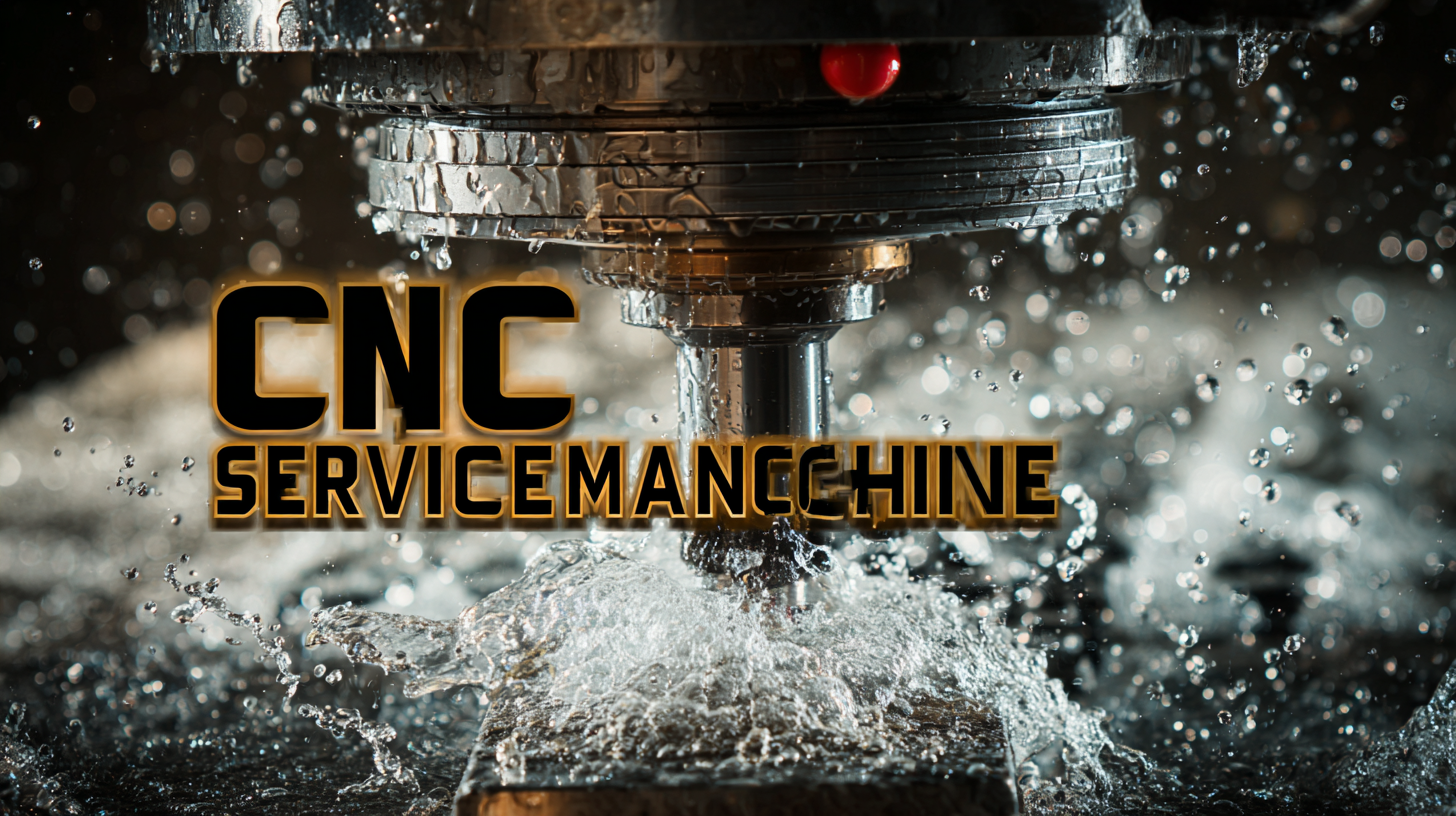
Furthermore, the emphasis on sustainability and eco-friendly practices is reshaping supplier selection criteria. A survey conducted by Deloitte found that 60% of manufacturers rank sustainability as a top priority in their procurement strategies for 2025. As such, quality suppliers must not only offer cutting-edge CNC services but also demonstrate a commitment to sustainable practices, such as energy-efficient machining and waste reduction. This dual focus on technological advancement and environmental responsibility will be pivotal for firms aiming to remain competitive in a rapidly changing market.
Key Features to Look for in Quality CNC Suppliers
When searching for quality CNC suppliers, certain key features can make a significant difference in ensuring a reliable partnership. First and foremost, look for suppliers with a strong track record in delivering precision and efficiency—essential attributes in today’s competitive CNC machine tools market. Suppliers that continuously innovate and adapt to advancements in technology, such as machine tool digitalization and smart manufacturing solutions, are at the forefront. This demonstrates their commitment to enhancing performance and meeting the evolving needs of various industries, from electrical to mechanical applications.
Additionally, consider the supplier's range of machinery and specialization. A supplier that offers a diverse array of CNC machines tailored to specific applications, such as cutting and engraving, can provide greater flexibility and meet unique production requirements. Beyond equipment variety, the availability of comprehensive support services and expertise in handling both standard and bespoke solutions is crucial. As the market for CNC machines is projected to grow significantly, partnering with suppliers who excel in customer service and technical support will ensure a smooth integration of their technologies into your operations, ultimately driving more value to your manufacturing processes.
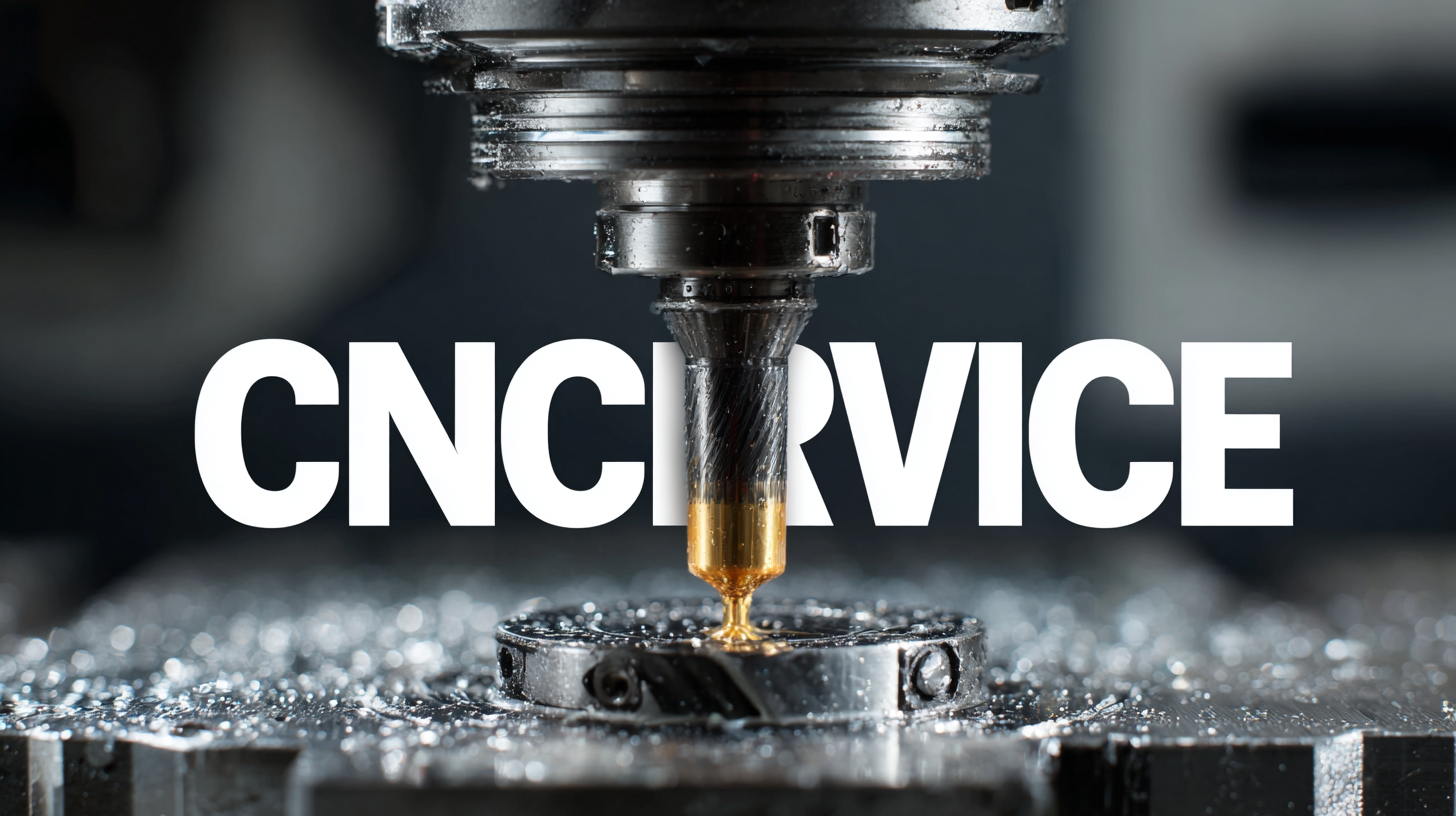
Exploring Alternative Technologies to Traditional CNC Machining
In the realm of manufacturing, the quest for quality suppliers often leads to exploring alternative technologies that can complement or even surpass traditional CNC machining. Techniques such as 3D printing and laser cutting are gaining traction for their unique advantages. These methods can significantly reduce lead times and waste, making them appealing options for businesses aiming to enhance efficiency.
When considering alternatives to CNC machining, it's crucial to assess the specific needs of your project. Understanding the materials you intend to use and the complexity of the components is vital. Here are a couple of tips:
1. **Evaluate the Technology**: Before making a switch, thoroughly research different technologies that could meet your requirements. Each method has its strengths—for instance, 3D printing excels in creating intricate designs, while laser cutting is ideal for precise, flat materials.
2. **Find Specialized Suppliers**: Look for suppliers who specialize in these alternative technologies. Their expertise can provide valuable insights and ensure you utilize the process that best suits your production needs. Engaging with suppliers who have a proven track record can also help mitigate risks in quality and consistency.
By understanding and leveraging these alternative technologies, businesses can stay ahead in a competitive market while ensuring high-quality outcomes.
Unveiling the Secrets to Finding Quality Suppliers for Best CNC Machine Service - Exploring Alternative Technologies to Traditional CNC Machining
Supplier Category | Technology Type | Service Offered | Quality Rating | Average Lead Time (days) |
---|---|---|---|---|
Metal Fabrication | 3D Printing | Prototype Manufacturing | 4.5 | 10 |
Plastic Injection Molding | CNC Machining | Custom Parts Production | 4.2 | 15 |
Woodworking | Laser Cutting | Furniture Manufacturing | 4.7 | 7 |
Electronics | 5 Axis Machining | Circuit Board Production | 4.8 | 12 |
Textiles | Computerized Embroidery | Custom Apparel Design | 4.0 | 20 |
Building Lasting Relationships with CNC Suppliers for Optimal Service
Building lasting relationships with CNC suppliers is crucial for achieving optimal service and ensuring quality outcomes. The CNC machining industry thrives on partnerships that foster trust and collaboration. Recent analyses show that companies investing in strong supplier relationships report a 20% increase in efficiency and a marked reduction in production delays. As the landscape of manufacturing evolves, particularly in sectors like medical devices, organizations are keen on identifying true partners who prioritize mutual success over transactional relationships.
To effectively collaborate with CNC suppliers, consider the following tips:
1. **Open Communication**: Establish clear and continuous communication channels with your suppliers. Regular check-ins can help address issues before they escalate and encourage the sharing of insights on best practices.
2. **Invest in Training**: Many suppliers benefit from training sessions that focus on product specifications and workflow efficiencies. By investing in these programs, you deepen your relationship and ensure that both parties are aligned on quality standards.
3. **Performance Metrics**: Set mutual performance metrics to gauge the effectiveness of your partnership. Monitoring these metrics can inform continuous improvement efforts and foster a competitive but cooperative environment.
By focusing on these key elements, businesses can navigate the complexities of the CNC machining supply chain and drive optimal service outcomes.
Quality Suppliers for CNC Machine Service
This bar chart represents the quality ratings of various CNC machine service suppliers, highlighting the importance of choosing reliable partners in the industry for optimal service delivery.
Evaluating Supplier Performance: Metrics that Matter in 2025
In 2025, evaluating supplier performance will be critical for businesses seeking to optimize their CNC machine service. Metrics such as on-time delivery, defect rates, and responsiveness will be pivotal in determining supplier reliability. According to a recent report by MarketsandMarkets, 70% of industrial companies cite supplier performance as a significant factor impacting their operational efficiency. By thoroughly assessing these metrics, companies can ensure that they partner with suppliers who not only meet production deadlines but also maintain high-quality standards.
Another key metric to consider is the Total Cost of Ownership (TCO), which encompasses not just the purchase price but also maintenance, logistics, and potential downtimes. A study by Gartner revealed that organizations focusing on TCO saw a 15% reduction in overall costs compared to those who primarily considered upfront pricing. As industries increasingly emphasize sustainability, evaluating a supplier's environmental impact will also become paramount. This holistic approach to supplier evaluation will empower businesses to forge stronger partnerships and enhance their competitive edge in the CNC machining landscape.