5 Proven Best Milling Equipment Options for Your Manufacturing Needs
In the dynamic world of manufacturing, choosing the right Milling Equipment is essential for optimizing production efficiency and ensuring product quality. With a plethora of options available in the market, it can be overwhelming for manufacturers to identify the best machinery suited for their specific needs. This guide aims to demystify the selection process by presenting five proven milling equipment options that cater to various manufacturing requirements.
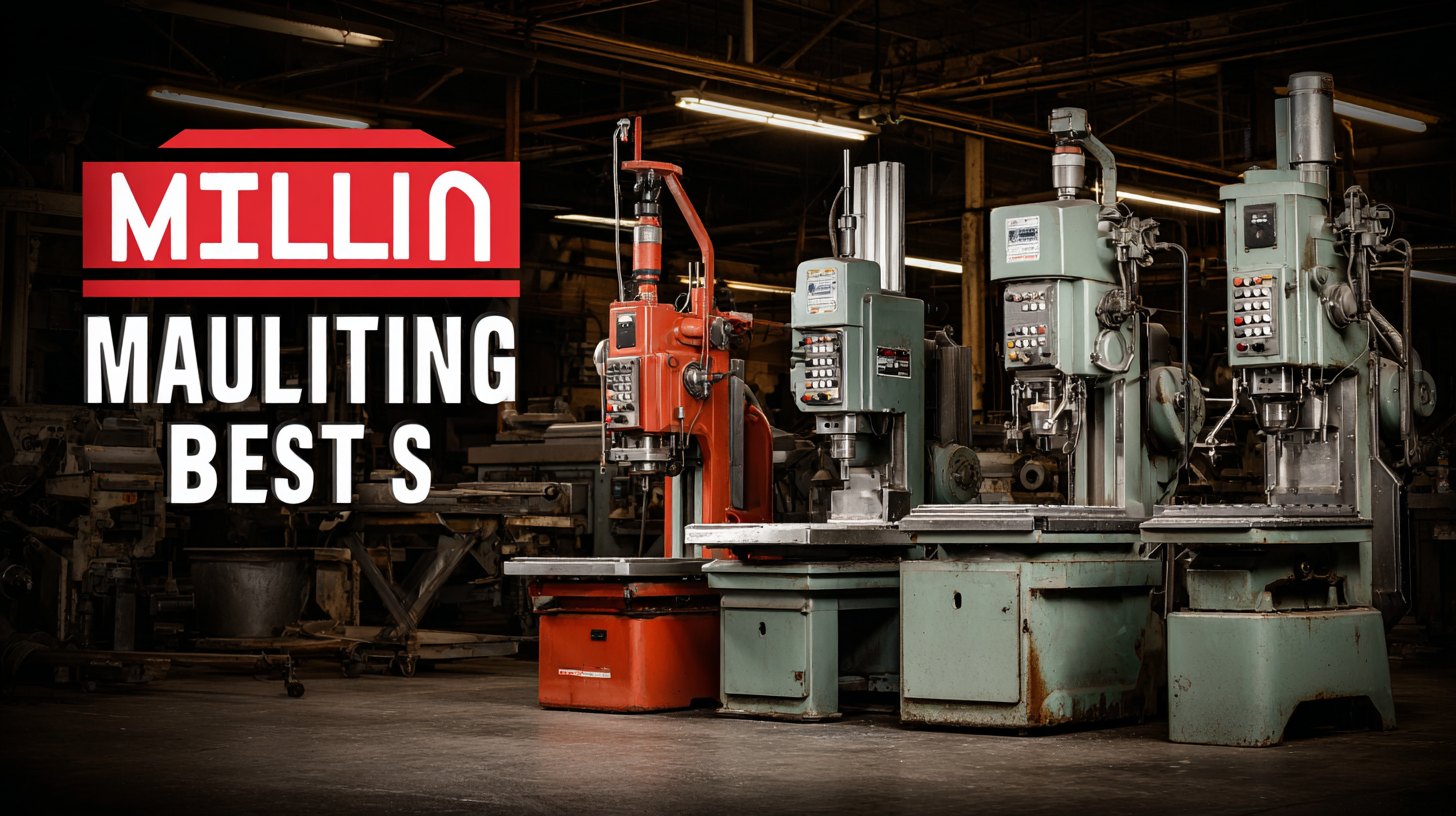
By understanding the fundamental differences and unique features of these milling machines, manufacturers can make informed decisions that enhance their operational capabilities. Whether you are a small business looking to scale up or a large enterprise aiming for precision, mastering the ins and outs of milling equipment will empower you to boost productivity and achieve your manufacturing goals.
Understanding the Importance of Milling Equipment in Modern Manufacturing
Milling equipment plays a crucial role in modern manufacturing, serving as the backbone for numerous production processes across various industries. According to a report by IBISWorld, the milling machinery manufacturing market alone has seen steady growth, with revenues reaching over $3 billion in recent years. This is a testament to the increasing reliance on precision milling to enhance product efficiency, reduce waste, and improve overall quality. The ability of sophisticated milling machines to achieve tighter tolerances and more complex geometries is essential for meeting today’s rigorous industry standards.
When selecting milling equipment, it is essential to consider the specific needs of your operation. For instance, CNC milling machines have become indispensable due to their versatility and automation capabilities. They can significantly reduce labor costs and manufacturing time. Tip: Always evaluate the technological advancements in milling options before making an investment; newer models can offer improved processing speeds and energy efficiency.
Additionally, the choice of milling equipment influences not only production efficiency but also the environmental footprint of a manufacturing operation. Recent studies have indicated that upgrading to energy-efficient milling machines can lead to a reduction of up to 30% in energy consumption, promoting sustainable practices. Tip: Implement regular maintenance schedules to ensure optimal performance of your milling equipment, which can also extend the machinery’s lifespan and further reduce operational costs.
Top 5 Milling Equipment Options Based on Industry Performance Metrics
In today's fast-paced manufacturing environment, selecting the right milling equipment is crucial for optimizing production processes. The focus on industry performance metrics highlights how advanced technology and data analytics can significantly drive the efficiency of milling operations. Utilizing Key Performance Indicators (KPIs) tailored to specific manufacturing needs allows companies to monitor their processes effectively. This approach, adapted from insights shared in the mining industry, underscores the importance of adopting analytics to enhance decision-making at all levels of the organization.
Among the top milling equipment options, five-axis machining centers stand out for their versatility and precision. These machines not only improve operational efficiency but also cater to the evolving demands of diverse sectors. By leveraging data intelligence, manufacturers can gain insights into equipment performance, ultimately refining their quality management processes.
With the right KPIs in place, businesses can benchmark their performance, leading to continuous improvement and enhanced cost competitiveness in a rapidly changing landscape. Embracing these tools and metrics will ensure manufacturers stay ahead of the curve and meet their unique operational demands.
Comparative Analysis: CNC Milling Machines versus Conventional Milling Equipment
When considering milling equipment for your manufacturing needs, a comparative analysis between CNC milling machines and conventional milling equipment is crucial. CNC (Computer Numerical Control) milling machines offer unparalleled precision and automation. They are programmed to execute complex tasks with minimal human intervention. This capability significantly reduces production time and enhances product consistency, making them a popular choice for high-volume manufacturing.
In contrast, conventional milling machines rely heavily on manual operation. While they may not match the speed and precision of CNC machines, they excel in versatility and cost-effectiveness, especially for smaller production runs or custom jobs. Operators can easily adjust settings and techniques based on specific project requirements, which can be advantageous when dealing with varied materials or intricate designs.
Tips: When selecting between CNC and conventional milling, consider your production volume and the complexity of your designs. For large-scale operations focused on speed and precision, CNC machines are ideal. However, for flexibility and lower upfront costs, conventional machines may be more appropriate, especially in workshops where custom tasks are common. Additionally, investing in training for your staff can enhance the benefits you gain from either type of milling equipment.
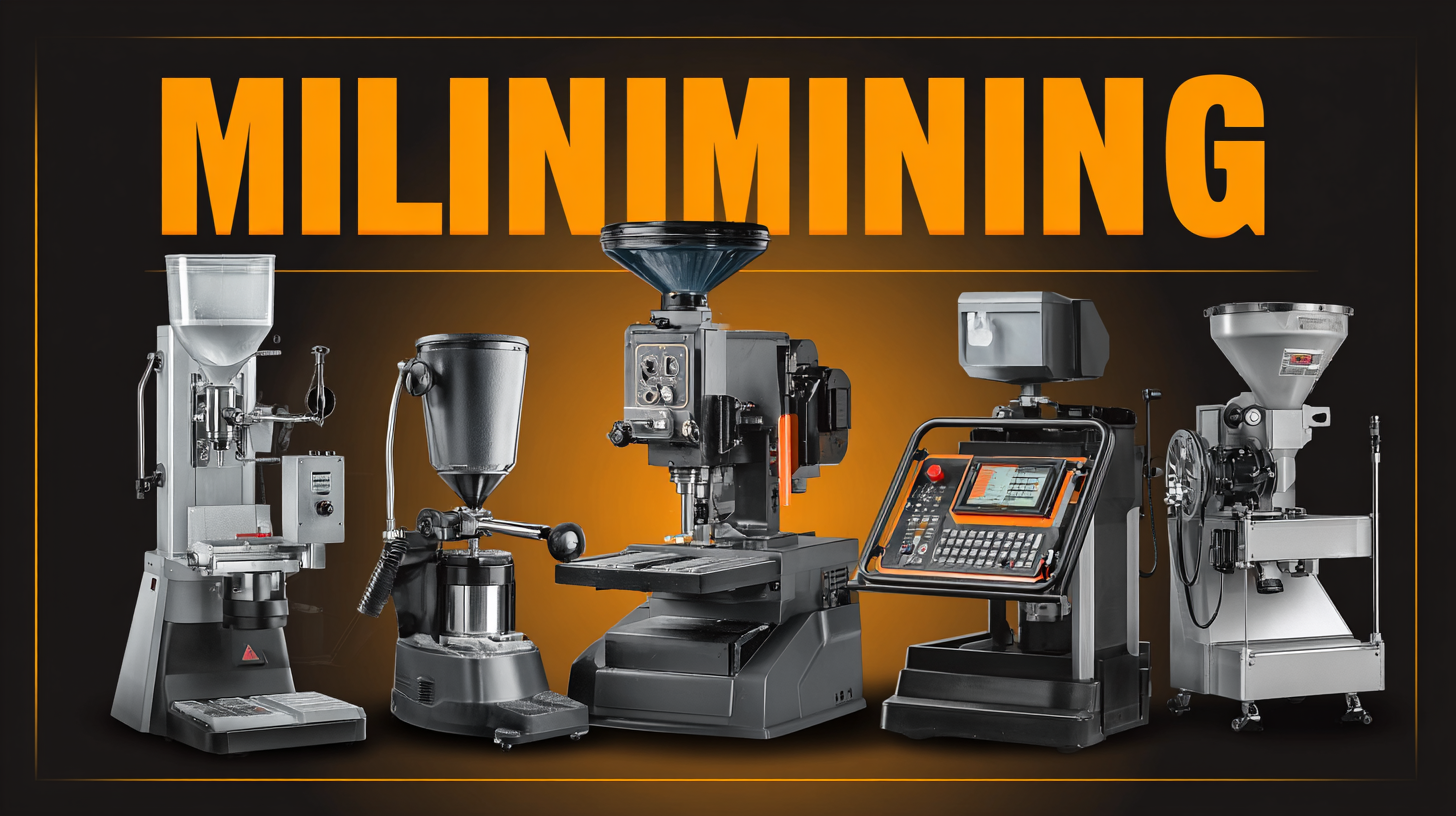
Key Features to Consider When Selecting Milling Equipment for Production
When selecting milling equipment for your production needs, it is essential to consider key features that will enhance efficiency and quality. One crucial aspect is the technology incorporated into the milling machinery. With advancements in data modeling and computer technology, CNC milling machines now utilize sophisticated data model-based toolpath generation techniques, significantly improving precision and reducing surface roughness in finished parts. This is particularly important in industries where surface quality is a critical measure of machining success, such as in die steel processing or dental applications.
Another important factor is the type of milling process suitable for your specific needs. For example, the choice between stone milling and roller milling can greatly affect the quality of flour produced in the food industry, influencing the dough rheology and the characteristics of the final bread product. Additionally, understanding the advancements in milling technology, such as those seen in dental milling machines, which are experiencing significant market growth, highlights the need to stay updated on equipment innovations that can cater to evolving manufacturing demands. Evaluating these features will ensure you select the right milling equipment tailored to your manufacturing objectives.
Future Trends in Milling Equipment Technology: What to Expect Beyond 2023
As we look towards 2024 and beyond, the future trends in milling equipment technology signal a transformative phase for the manufacturing sector. Notably, advancements in AI and robotics are expected to revolutionize milling processes, enhancing precision and efficiency. A recent report indicates that AI applications in manufacturing could save companies over $1.5 trillion by 2024. Furthermore, the growing adoption of smart manufacturing will see the integration of real-time data analytics into milling operations, allowing manufacturers to optimize workflows and reduce downtime.
When considering these emerging trends, it's vital to stay ahead by investing in adaptive technologies. **Tip:** Evaluate milling equipment that supports IoT connectivity, providing insights into machine performance and maintenance needs. Additionally, as sustainability becomes a focus, explore options that incorporate energy-efficient designs to minimize environmental impact.
Moreover, the rise of technologies such as 3D printing is reshaping the landscape of parts production and prototyping in milling. Industry experts predict that by 2023, 70% of manufacturers will integrate some form of additive manufacturing into their processes. **Tip:** Familiarize yourself with hybrid milling solutions that combine traditional methods with additive capabilities to enhance productivity and material utilization. This proactive approach will ensure that your manufacturing operations remain competitive and aligned with future trends.
5 Proven Best Milling Equipment Options for Your Manufacturing Needs
Milling Equipment Type | Key Features | Material Compatibility | Expected Trends Post-2023 |
---|---|---|---|
CNC Milling Machines | High precision, programmable, multi-axis | Metals, plastics, wood | Increased automation, AI integration |
Vertical Milling Machines | Simple design, versatile, easy tool access | Metals, composites | Smart controls, cloud connectivity |
Horizontal Milling Machines | Powerful cutting, larger workpieces | Heavy metals, structural components | Enhanced safety features, energy efficiency |
Bed Milling Machines | Strong stability, large work area | Metals, larger assemblies | Adaptation to smart technologies |
Universal Milling Machines | Versatility in operations, adjustable features | Various metals and non-metals | Sustainability initiatives, greener technologies |